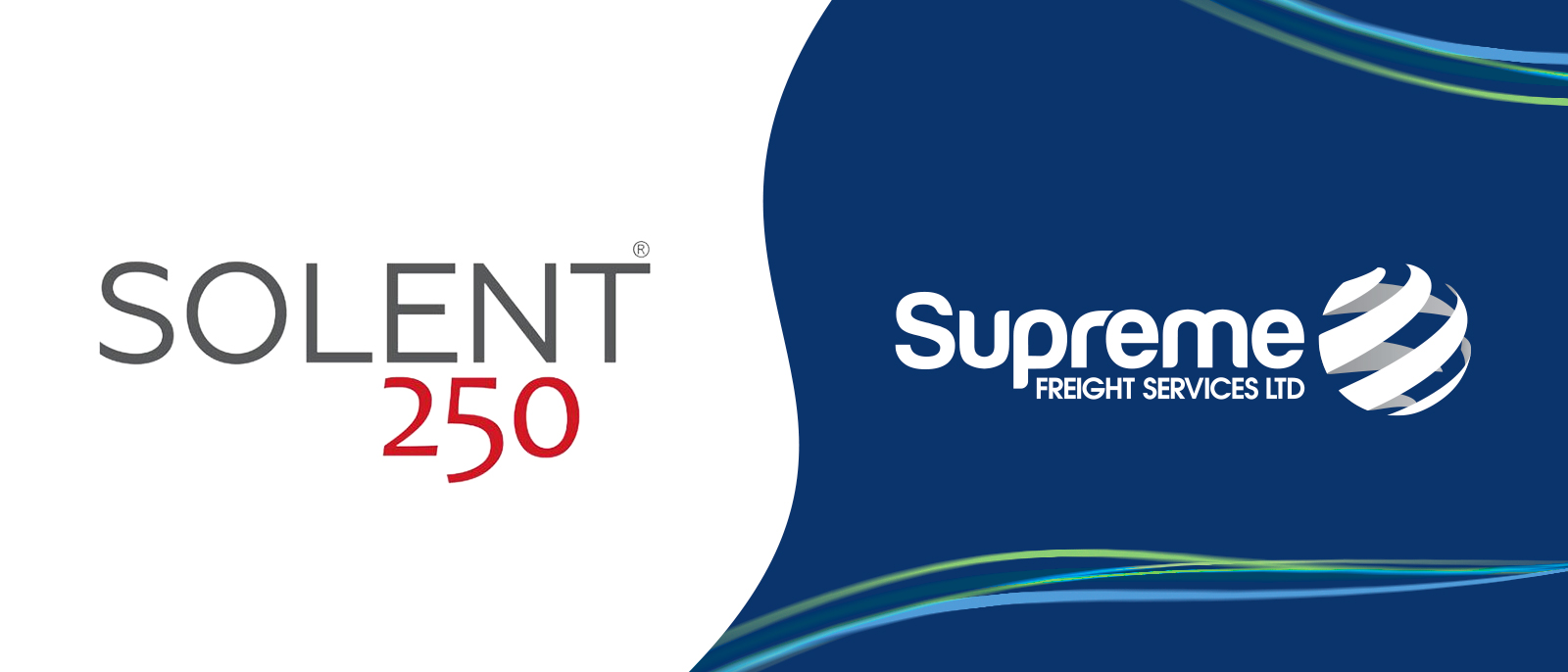
We are very proud to announce that we are again featured in the Solent 250 - and this year we are in the top 40!Earning a place on this list is a huge achievement & we would like to take this opportunity to thank all our incredible members of staff & our loyal customers for…