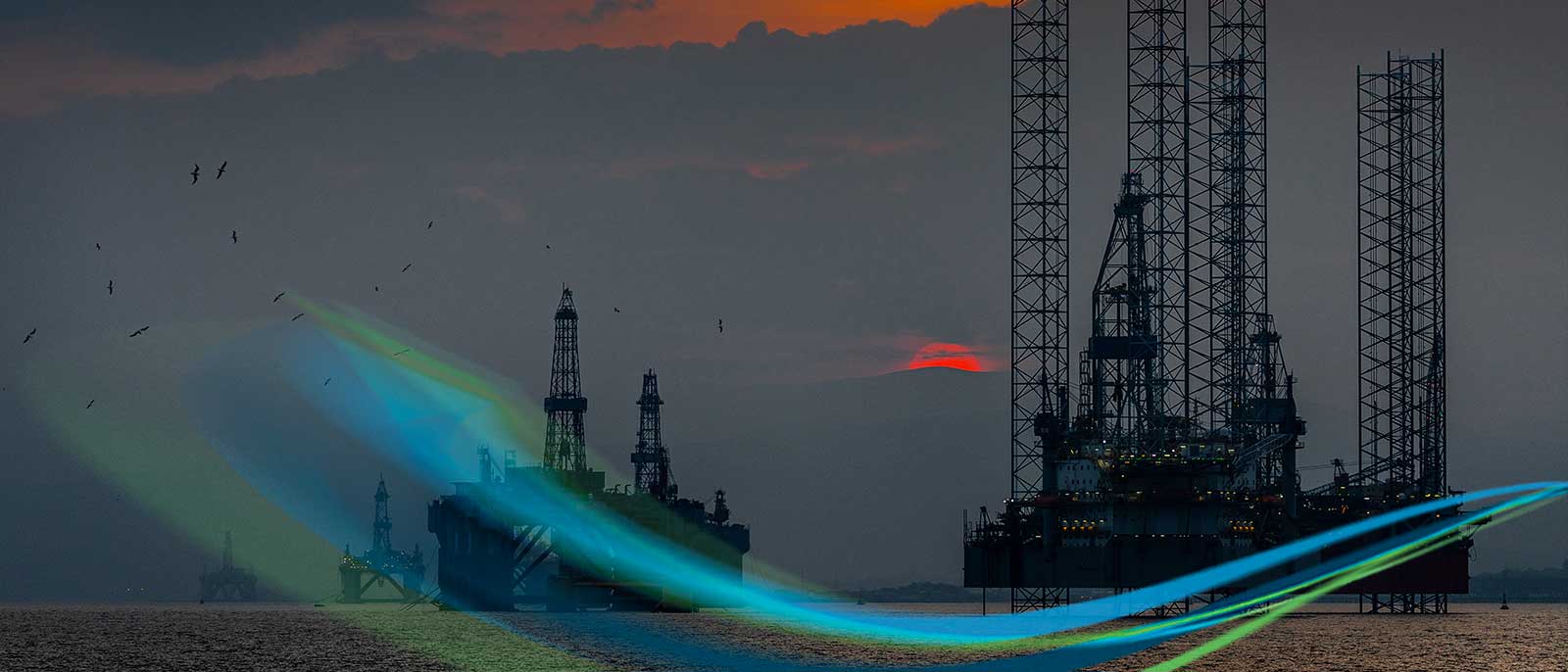
Ports across the world are highly reliant on fossil fuels so decarbonising them will require significant planning and investment. But the process to make our ports more sustainable is becoming clearer. Identifying causes of pollution Cargo ships, cruise ships, trains, cranes, fuelling systems, tugs and port vehicles are all contributors to the total emissions that…