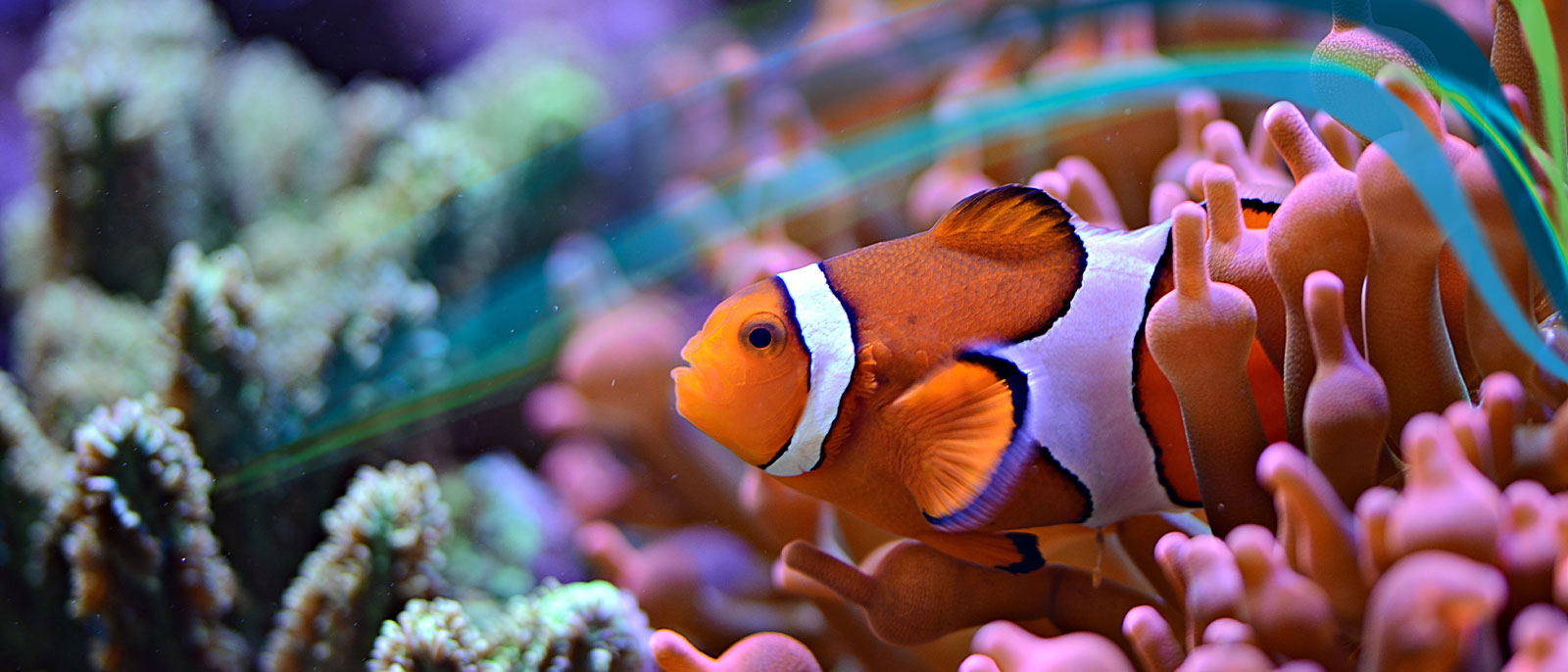
There are three main types of marine insurance, ship or hull insurance, cargo insurance and freight insurance. There are many benefits to purchasing marine insurance, especially when dealing with goods. What is it? Marine insurance provides coverage against any losses that can occur from unforeseen events while at sea. Marine insurance can provide cover for…